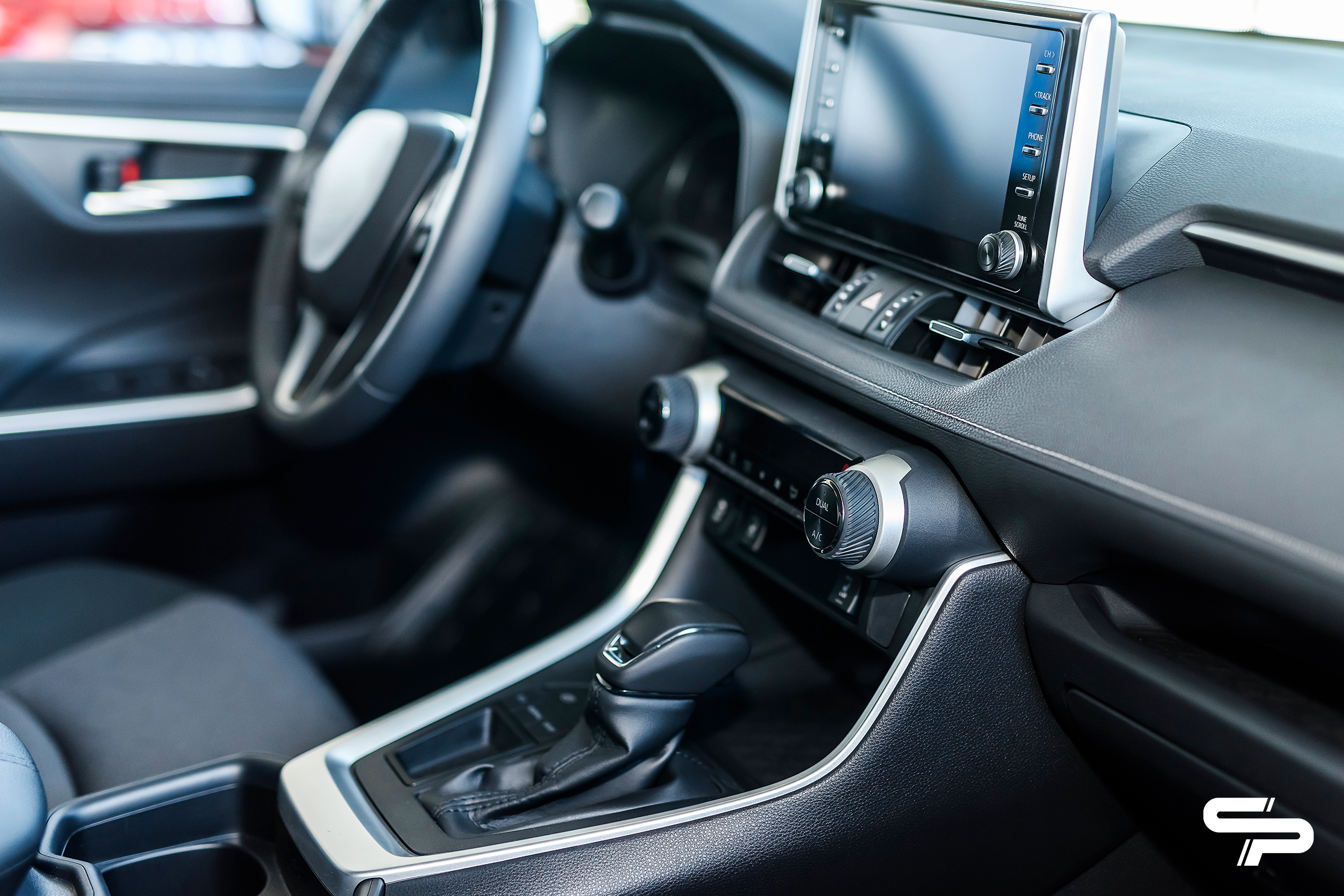
Quality Precision
As automotive technology continues to advance, these changes promote the development of more complex and technically challenging injection molded components. Within these components are intricate processes and materials. Chemtech looks to support automotive industry clients in creating these complex components. With our in-house mold design, CAE mold simulation software, DFM analysis, a dedicated project engineer, APQP, and additive in-house 3D printing. This blog will discuss how we fulfill components and the processes that go into them.
At Chemtech Plastics, we produce several automotive components:
- Accelerator pedals
- Rain LT sensor
- Throttle by wire switch
- Optical lenses
- Occupant safety systems
- Lever stalks
- Multifunction switches
- Power window switches
- Directional components
- Light pipes
- Automotive fuel system components
- Audio/in-ear monitoring
Rain LT Sensor
The Rain Light Sensor is a 3-shot (3K) component that is used across multiple vehicle platforms. This component provides signals to enable headlights and windshield wipers, adjust HVAC temperatures, deploy Driver Assist, and other safety functions.
This mold requires a challenging 0.2-gram shot weight of clear resin portion. A specialized molding cell is specifically sized for this application. The mold opens once the first and second materials are injected into the mold. These two molded components are then rotated into position for the third material to be injected.
Following the process, the parts are retrieved and transported by robots into thermoformed trays designed for this application. This part is then inspected for blemishes or imperfections as it’s an optical surface. Chemtech has supplied this part for over 10 years, defect-free.
Junction Relay Box
The junction relay box is a complicated component, as it includes over 100 terminal pockets, and it can be difficult to get the material to flow into these small locking features.
As a part of the molding requirements, the Junction relay box requires hundreds of small mold inserts with very tight dimensional requirements. These inserts are extremely fragile and have a unique design.
The shut-off between two of these inserts can be a quarter-degree shut-off angle requiring the inserts to be machined and held in positions to within one ten-thousandth of an inch (0.0001). Maintaining and assembling these tools require a special level of skill.
2-Shot Housing Cover
Our 2-shot (2K) housing cover is used to contain the accelerator pedal for the throttle-by-wire system, which we can also produce. This part requires a specialized molding press to have the second material in the mold’s cavity and core side.
This is accomplished through a rotating center plate that captures a small portion of the exterior surface. The plate transports the first shot to the second shot position. In this position, both new cavity and core details are located in the first shot.
Further complexity comes from the first shot resin that is 50% glass-filled polypropylene and 10 mm long glass fibers. This material can be abrasive and cause steel wear. A specific aerospace plating is applied permanently to the mold surface to counteract this.
Chemtech Advantage
The Chemtech team works closely with automotive manufacturers to design and manufacture high-quality components. Our utilization of cutting-edge technologies and methodologies enables us to fabricate precise, lightweight plastic injection-molded components. These components have applications across diverse automotive sectors, encompassing interior and exterior trim, lighting systems, engine elements, and more.
Ready to see what Chemtech can do?
Let’s start a project together. Request your free quote today.