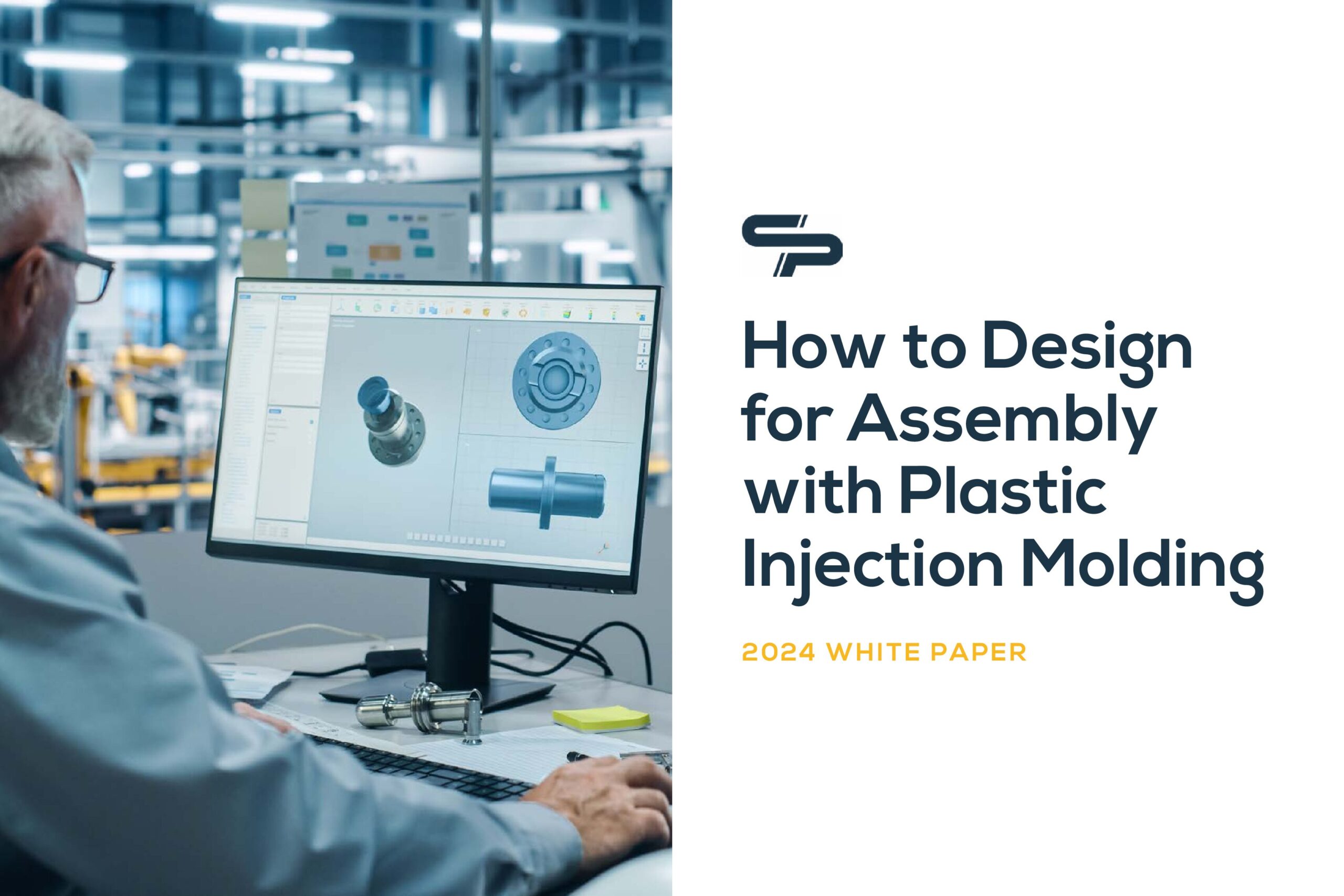
OVERVIEW
Every manufacturer wants to create the most efficient processes at the lowest cost. But how do you get there? One crucial methodology to apply to your manufacturing process is Design for Assembly (DFA). Designing for Assembly means that you consider questions like how many parts are incorporated into your assembly process, how many people are working on it, and how long it will take to bring a product to market. The end result after applying all of these considerations is a personalized and streamlined assembly process.
This article will explain what DFA is, illustrate why it’s important, list the five pillars of DFA, describe how DFA applies to plastic injection molding, and share how Chemtech Plastics utilizes DFA.
WHAT IS DFA?
DFA is a product design methodology that helps manufacturers develop products that can be assembled more easily. 1 It is a core consideration in the design process. DFA aims to effectively reduce production and labor costs, time, and any challenges that may arise during the assembly and manufacturing processes.2
DFA was first developed by Geoffrey Boothroyd, a professor at the University of Massachusetts Amherst, in the late 1970s.3 DFA is implemented from the very beginning of the manufacturing design process; Boothryod states that the goal of DFA is “to create a clearly defined procedure for evaluating a design with respect to its ease of manufacture and assembly,” and this is achieved by “providing manufacturing input at the conceptualization stage of the design process in a logical and organized fashion.”4
In order to meet these goals, those employing the DFA process look for ways to design parts that are easy to assemble and disassemble, parts that are interchangeable, an assembly process that is simple, and a product that is safe to assemble and use.1
WHY DFA IS IMPORTANT
According to John Linder, Director of Sales and Marketing at plastic injection molding company Chemtech Plastics, DFA is important because products that undergo this process are more reliable and have better overall quality than their counterparts that were not designed based on a DFA review. Due to their superior quality, DFA-reviewed products tend to be easier to maintain, requiring less repairs over time.
DFA is also an essential component to ensure product safety. DFA designers employ automation into the product design process, most commonly at the final assembly stage, to reduce variation that often comes with human error, thus increasing consistency. Greater variability between copies of the same product can lead to a greater range of performance results – including the potential for more products to perform outside the intended function of the product. As the product performance range rises, the potential of the product acting in unexpected ways also rises. This is where safety issues emerge. The more accurately and repeatedly a product is manufactured and assembled, the safer and more reliable the product will be.1
THE FIVE PILLARS OF DFA
DFA can be distilled down to five pillars: reducing part count, modularizing and standardizing, symmetry and concentricity, streamlining the assembly process, and mistake proofing.5
REDUCING PART COUNT
Finding ways to reduce the number of parts is the first step in DFA, and is widely considered to be the most impactful. Reducing the number of components in a product simplifies the product’s structure – and by extension, its assembly process. A simpler process is more easily repeatable. In addition, incorporating fewer parts equates to less materials, inventory, handling, tooling, and maintenance costs for the product. For example, it’s simpler and more cost-effective to design a bottle cap as a single piece than a separate seal and cap.6
There are a few pivotal questions to ask during this step:
Is this part really necessary? Quite often, extra parts are included “just in case” during development and are never eliminated in the final product design.
Can this part’s primary function be done by a different part? Avoiding redundancy is key.6
A common way to address these questions is by performing an analysis of part count efficiency. Apply the above questions to your parts to determine which are essential (necessary for function) and non-essential (parts that can be eliminated without affecting the product’s function). Realistically, no product can be solely composed of essential parts, so it’s best to aim for an efficiency of around 80%.6
MODULARIZING AND STANDARDIZING
In product design, modularizing involves dividing a product into a collection of independent modules that can be easily assembled, disassembled, and replaced. Modular design allows for parallel assembly, mass customization, easier testing, and easier repair.6
For an easily understandable example of modular design, picture the sectional couch – one defined unit (the couch itself) that can be taken apart and rearranged according to the owner’s preference.7 Another good example is the laptop computer: one complete unit that has interchangeable parts such as a screen, keyboard, and hard drive.6
Standardization goes hand in hand with modularity. Creating a standard process for parts assembly simplifies the transfer from design to production by making the assembly familiar and facilitating a readiness to ramp up production. Additional benefits of standardization include faster development, easier training for assembly line workers, reduced inventory costs, and more predictable and reliable product quality.8
SYMMETRY AND CONCENTRICITY
Another way to simplify a product is to design it with symmetrical parts. Symmetrical parts can be oriented in any way during assembly, which reduces the need for reorientation as well as verification checks on alignment and orientation. For example, a cylindrical battery can be inserted into a battery holder in any direction.6
Concentricity is a significant factor in product symmetry. When multiple parts are concentric, it means that they have the same center point. Concentricity ensures the production of symmetrical and dimensionally accurate parts through molding and casting processes as well as proper fit and function of components during assembly, which prevents binding, leaks, and other issues.9
For products that cannot be made symmetrical, it’s best to go as far in the complete opposite direction as possible and design products with obvious asymmetry; for example, if a part can only be mated in one way, designing the part in a way that makes it extremely clear which way to mate a part will reduce the likelihood of mistakes.5
STREAMLINING THE ASSEMBLY PROCESS
There are a number of additional DFA considerations that can make the assembly process smoother. For example, parts should be easy to handle and join. In order to achieve this, parts should be designed to have as few handling steps as possible. Parts should also be easy to handle with no sharp edges or burrs and should utilize self-aligning and self-locating pieces. For example, a couch can be designed with pre-drilled holes and screws that are easier for the assembler to access and tighten.6
MISTAKE PROOFING
Most competitive studies have found that 70-100% of manufacturing incidents occur due to human error.10 Therefore, it’s imperative to design parts and assembly processes that prevent or detect errors and defects. Whenever possible, DFA designs should incorporate features like color-coding, one-way assembly, or unique shapes to prevent human error during assembly.5
DFA AND PLASTIC INJECTION MOLDING
DFA is well suited for plastic injection molding, since most plastic molded components are not standalone, discrete items, but rather components used in a larger assembly. 1 Think of fuel pedals for cars or robotic surgical components, for example.
A vital step when applying DFA for molded components is to bring the molder into the product design process early in the design phase, before design freeze (the point in the design process when all major and critical components and materials in the product and manufacturing, assembly, and testing processes are finalized, or “frozen”).11 There is little opportunity to implement ideas that improve a design once it is frozen.
Bringing the injection molder into the DFA process means that the molder understands the entire assembly and how the assembly is designed to function. Savvy injection molders can use this knowledge to offer suggestions and solutions for incorporating items, such as snap features, into the design to reduce the number of purchased components. Adding snaps or other items like alignment ribs can reduce overall cost and assembly times. This is only possible if the molding partner is brought into the product design process early on.1
Injection molders can also help determine how to best utilize automation. Precision plastic injection molders like Chemtech Plastics use automation in many types of assembly applications; how to best use automation is different for each project. When the project volume is high, more sophisticated and complex automation technology can be used to perform the assembly and testing operations. It becomes more challenging for the injection molder when the number of parts being produced drops below a threshold where more sophisticated automation can be cost justified. A DFA analysis needs to be conducted to ensure a cost-effective solution.1
DFA AND CHEMTECH PLASTICS
For over four decades, Chemtech Plastics has been an industry-leading, full-service precision injection molding company; we are both DQS-Certified for IATF 16949 : 2016 and ISO 9001 : 2015. We are an engineering-driven company with countless years of experience in technical molding and mold making. Our state-of-the-art facility and dedicated team allow us to successfully take on tight-tolerance, critical-to-function projects from a variety of industries.
Chemtech Plastics applies Design for Assembly to every part and component that we produce. Every individual at Chemtech Plastics is dedicated to the creation of defect-free products and services. We regularly set new quality objectives to allow ourselves to measure and assess our own abilities and progress. Our ultimate goal is to achieve the highest level of quality across the board — from development and production to customer service and employee satisfaction.
We aim to plan, produce, and support the absolute finest injection molding components to serve leading automotive, medical, industrial, and optic lighting companies worldwide. Chemtech Plastics is on a mission to champion the highest quality injection molding products by efficiently delivering precision technology through absolute reliability and support to our clients, and DFA is a crucial step in this mission. Chemtech Plastics the solution to all of your injection molding needs.
1 John Linder, Director of Sales and Marketing, Chemtech Plastics
2 https://jiga.io/articles/design-for-assembly-principles-applications-guidelines/
3 https://www.machinedesign.com/automation-iiot/article/21213546/a-history-of-design-for-manufacturing-and-assembly
4 https://www.iqytechnicalcollege.com/BAE%20682-Assembly%20Automation%20&%20Product%20Design.pdf
5 https://www.fiveflute.com/guide/design-for-assembly-dfa-best-practices/
6 https://uark.pressbooks.pub/mechanicaldesign/chapter/design-for-assembly-principles/
7 https://www.shieldcasework.com/the-benefits-of-modular-products/#:~:text=What%20is%20modularity?,time%20is%20cut%20in%20half
8 https://jiga.io/articles/design-for-assembly-principles-applications-guidelines/
9 https://www.crossco.com/resources/glossary/metrology-glossary-concentricity/
10 https://fractory.com/poka-yoke-in-manufacturing/
11 https://www.lawinsider.com/dictionary/design-freeze#:~:text=of%20Design%20Freeze-,Design%20Freeze%20refers%20to%20a%20procedure%20where%20upon%20successful%20completion,shall%20be%20documented%20and%20frozen