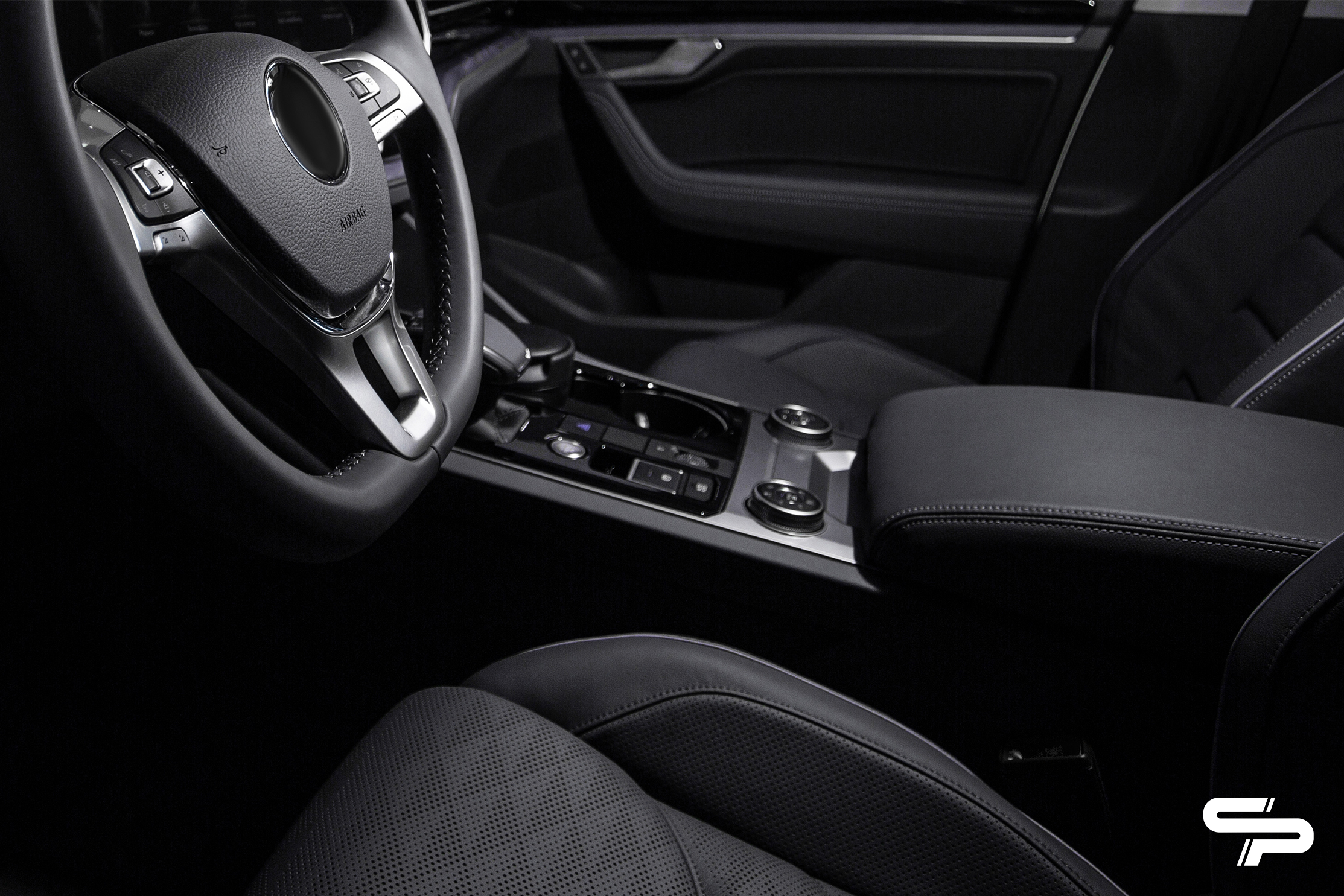
Plastic injection molding for the automotive industry requires high precision and high specificity to ensure the end product meets industry standards. How do you know which type of molding is best for your particular project?
This blog will guide you through the three most common types of injection molding used for automotive industry parts. Our aim is to simplify a highly complex topic and help you get on your way with your next automotive part project.
Straight Injection Molding
Straight injection molding is the most common type of plastic processing. This type of process is so common because it can be used to create large product volumes quickly, cost-effectively, and at a consistently high quality.
How does it work? The first step is to create a digital 3D part model using computer-aided design (CAD) software. Based on the part model, tool engineers create a mold design, and mold makers create the mold based on that design. Then, during production, molten plastic is injected into the cavity of the mold. The plastic then cools and solidifies, taking its desired shape. In the final step, the part is removed from the mold, and is now ready to move along in the product manufacturing process.
Straight injection molding is used in innumerable automotive industry parts like junction relay boxes, seat belt retractor mechanism components, and electronic enclosures.
Insert Molding
Insert molding is similar to injection molding. It also involves injecting molten plastic into a mold and uses the same type of plastic materials. The difference is that during the insert molding process, an insert (or multiple inserts) is added into the mold and becomes a permanent part of the end product. Insert molding is favored for its flexibility – the addition of inserts introduces a sharp increase in the possible number of product configurations for a part.
There are four main steps in insert molding:
- Similar to injection molding, a digital part model is made. For insert molding, designers must also consider where to add the insert to ensure that it retains its orientation and stays in place.
- The insert is added into the mold. This can be done through automation or manually. Typically, automation is used for high-quantity orders, and manual insertion is used for low-quantity orders.
- The molten plastic is injected into the mold, filling the mold and adhering to the insert.
- Once cooled, the molded part is removed from the mold. The part is complete and ready for the next step in production.
Insert molding is a common production process of automotive part manufacturing, such as sensor housings, switch components, and automotive electronic housings.
Multishot (2k/3k) Molding
The final molding process that’s popular for producing automotive parts is multishot molding. Multishot molding is used to create complex parts with multiple plastic materials. There are many types of multishot molding, but 2k and 3k are the most common.
In 2k molding, sometimes called two-shot or two-component molding, two different plastic materials are injected into a mold to make one part. In 3k (or three-shot or three-component) molding, three unique plastic materials are injected into one mold.
The process is the same as straight injection molding, with some extra steps: after the first material is injected into its cavity and cooled, the mold opens and rotates to the second cavity position, at which point the mold closes and a second material is injected into a second cavity. That’s 2k molding. For 3k molding, the process continues – the injected material is cooled, the mold opens and rotates, and a third material is injected into a third cavity.
Multishot molding is used to create a part with two or more distinctive features, like multiple colors or textures (e.g., hard outer shell and soft-touch inner surface). Parts made with multishot molding can be seen in many types of auto parts, like rain and light sensors, pedal arms, and instrument bezels.
Automotive Industry Molding at Chemtech
At Chemtech, creating specialized parts for the automotive industry is our specialty. With four decades of experience and a world-class facility, we are well-prepared to meet the rigid demands of the automotive industry for volume and quality. We employ custom molding machines, specialized material drying equipment, hot runner controllers, and mold temperature regulators to ensure that our equipment is easily able to perform to our automotive customers’ high expectations.
We apply this equipment on numerous materials that are commonly required in the automotive industry:
- Nylon (PA6 or PA66)
- Polyester (PBT)
- Polycarbonate (PC)
- Polycarbonate-ABS (PC/ABS)
- Polyoxymethylene (POM)
- Polyphthalamide (PPSU; brand name Radel®)
Chemtech offers straight injection, insert molding, and multishot (2k and 3k) capabilities. Contact us today to start your project.